DRY-CLEANING PRESSES Dry-cleaning presses have perforated metal heads and bucks through which steam is admitted by the operator. The heads are normally covered with a perforated, thin, metal mask, which is
sometimes also covered with a moleskin type of fabric to prevent a gloss on pressed articles. The bucks are usually padded and are then covered with a perforated metal mask and a cloth covering. Presses used for dry cleaning aboard ship are listed in the Navy Laundry and Dry-cleaning Catalog, NAVSEA S6152-B1-CAT-010. There are two general utility dry-cleaning presses listed, one made by Ajax and the other by
Florenta. The Ajax model is shown in figure 6-4. This model is very easy to operate. After dressing an article on the buck, the operator raises the head closing bar to close the head. Then, pressing the head locking handle with the other hand, the operator locks the head in the pressing position. Simply pressing the table-mounted release button will open the head at anytime. Steam can be provided to the head by pressing the steam handle located on the head, and buck steam and vacuum are supplied by depressing the two foot pedals. The Florenta dry-cleaning press uses the hand control buttons in conjunction with the safety control bar. The operator pushes the black buttons on each side of the worktable facing with
both hands. This will close the pressing head unless the safety control bar contacts an object or the buttons are released before the head is closed. To open the press head, the operator simply lifts up on the safety control bar and the press head will open to the full position. The two control buttons on the worktable facing are not used in the opening of the pressing head. The head steam and buck steam and vacuum are operated in the same manner as previously described. Synthetic uniforms should not be pressed on HOT HEAD presses (uncovered polished steel). Synthetics cannot withstand high temperatures and, therefore, should be done on a dry-cleaning press. Steam lines under no more than 75 to 80 pounds per square inch pressure should be connected to dry-cleaning presses. At this pres-sure the proper amount of moisture and heat is available to properly press the item of apparel. CAUTION is required in pressing fabrics containing high percentages of either Dacron polyester fibers or Orion acrylic fibers because control of temperature, pressure, and time is important. For best results 100 percent Dacron and Orlon fabrics should be pressed
at temperatures around 275 F with low mechani-cal pressure and short intervals of time. In blends of Dacron with wool, higher temperatures may be used provided the mechanical pressure and contact time are kept at a minimum. Improper pressing techniques may result in a shiny, watered, clouded, or frosted
appear-ance, needle holes, and difficulty in alter-ing the finished garment at some later date. If high steam pressures are used, it is doubtful that pressed seams can subsequently be altered. Permanent damage results from the defects discussed above because they can-not be removed by sponging or other treat-ment. PRESS LAYS In machine pressing, each garment is finished by a series of lays. Each lay is a position of the garment on the buck, and the series should cover the entire garment. Places on the garment that cannot be pressed with the machine should be smoothed out by inserting a puff (pad) and pressing the spot against the head of the press or
by using a hand iron. All pressers do not follow the same pattern for pressing the same article. Generally there is not much variation in different lays. Sequences of lays for trousers tops and legs, jumpers, and uniform coats are described in the following pages. The ones given are considered the minimum for each article when high-quality pressing is desired. Trouser Tops Figure 6-5 gives the sequence of lays for pressing trouser tops. With the fly open (lay No. 1), draw the left trouser top over the small end of the buck, having the fly front almost even with the front edge of the buck. Steam by using the head and applying light pressure, then dry thoroughly with the vacuum. Again place the left trouser top on the small end of the buck as shown in lay No. 2. The pocket should be in the center of the buck. Straighten the pocket and make certain that the outer edge is even and drawn together. Steam, press, and dry the lay. In lay No. 3, the left side pocket is even with the front edge of the machine and the back center seam is even with the rear edge of the buck. The left hip pocket lies in the center of the buck. Steam the material lightly and pull the pocket together. In making lay No. 4, draw the trouser top over the small end of the buck so that the end of the buck fits well down into the seat of the trousers and the back seam is directly in the center of the buck. Apply steam and light pressure and vacuum dry. In making lay Nos. 5, 6, and 7, continue on around the trouser top, pressing the right side. These lays are not shown as they correspond closely to lays 3, 2, and 1.
Figure 6-5.-Lays for pressing trouser tops. When available, the automatic topper press may be used to press trouser tops. The topper press eliminates the need for lays discussed above and also speeds up production. This type of press is discussed later. Trouser Legs Lays for pressing trouser legs are given in figure 6-6. The first step is to place the front portion of the left leg on the buck- crotch at the large end, the inside of the leg facing upward, the seams lying on the center of the buck (see lay No. 1). Make sure that one seam rests upon the other for the entire length of the leg. Apply steam to soften the material and straighten the knee. Lay the left leg, as shown in lay No. 2, on the front of the buck so that the front crease is in the center of the buck and the top of the trouser is at the large end of the buck in a line with the second or third button of the fly (or, if zippered, 2 or 3 inches from the bottom) in position so the crease will extend upward as far as possible. In lay No. 3, move the trouser leg to the rear of the buck so that the back crease is lying on the center of the buck. The leg should be placed so that at least 4 inches of the seat will be creased. Extend the crease as high as possible without wrinkling the crotch. Lay Nos. 4 (right leg, front portion), 5 (right leg front crease), and 6 (right leg rear crease) are substantially the same as lays 1, 2, and 3 of figure 6-6. Uniform Coats Check figure 6-7 (lays 1 through 6) and figure 6-8 (lays 7, 11, and 13) for the lays used in pressing uniforms coats. Place the left side of the coat collar and the left lapel on the rear of the large end of the buck and press as shown in lay No. 1. This operation shrinks the collar at the gorge seam, restoring the shape of the garment where it tends to stretch, from the seam at the shoulder down to about 5 inches below the gorge seam. Lay No. 2 is similar to lay No. 1 except that the right side of the collar and the right lapel are pressed. Make this lay on the front of the large end of the buck. Lay Nos. 1 and 2 serve to restore the balance of the coat so that the left front and right front hang evenly. After creasing the two sides of the collar, place the collar on the large end of the buch (see lay No. 3) so that the center is on the center line of the buck. In most cases the collar is stretched while
Figure 6-6.- Lays for pressing trouser legs.
Figure 6-7.-Lays 1 thrugh 6 for pressing uniform coats.
Figure 6-8.-Lays 7, 11, and 13 for pressing uniform coats. being worn. Distribute the extra fullness over the length of the collar and steam freely. In lay No. 4, place the right front of the coat at an angle to bring out the chest. Never stretch the front of the coat; gather in the front slightly and shrink it to the proper length. Steam well before applying pressure, then vacuum dry. See that the pocket is smooth. Move the coat forward on the buck for lay No. 5. The small end of the buck fits into the chest about 1 inch below the armhole pit and within 2 or 3 inches of the side seam. Any fullness on the dart seam should be taken in between the pocket and the armhole pit. In lay No. 6, place the right half of the back on the buck so that the lay is about 1 inch from the right armhole and about 2 inches below the collar. The side seam slants in from the armhole;
the bottom of the seam is about 4 inches from the front edge of the buck. The center seam in the back of the coat should be placed in the
center line of the buck for lay No. 7 (fig. 6-8). See that the bottom edge of the under collar is placed even with the edge of the buck. Any fullness in the center seam between the shoulders should be taken in.
Continue on around the coat, making lay No. 8 (left half of coat back), lay No. 9 (left side and pocket), and lay No. 10 (left front edge) to correspond to lays 6, 5, and 4.
Place the right facing of the coat fronton the buck, facing up as shown in lay No. 11. This lay takes in the coat edge from the bottom of the coat
to a point below the gorge seam. Lay No. 12, for the left facing, is the same as No. 11. Insert the sleeve former as shown in lay No. 13 and place on the buck of press. Bring the press head down for light contact only and steam from the head and the buck and then apply vacuum until dry. Turn the sleeve over without removing the former and repeat on the other side. The same methods are applied for the right sleeve. Visible creases from previous pressing can be removed by rubbing on the buck and steaming with the former still in the sleeve. For stubborn creases,
wet with a damp cloth, allow to dry, and press as above. Fit the shoulder pad into the sleeve head at the back seam. After spreading the fullness evenly, apply steam and then hold lightly against the head allowing the heat to press out the fullness. Next follow around to the front of the sleeve, getting in far enough to take care of the wrinkles. Work out the wrinkles in the other shoulder. Dry-cleaning plants on board some Navy ships
are equipped with a steam air finisher. This equipment can be used to do suit coats and increase work output. This equipment is discussed later in this chapter.
|
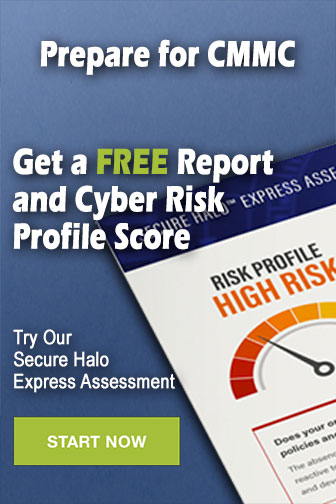
|